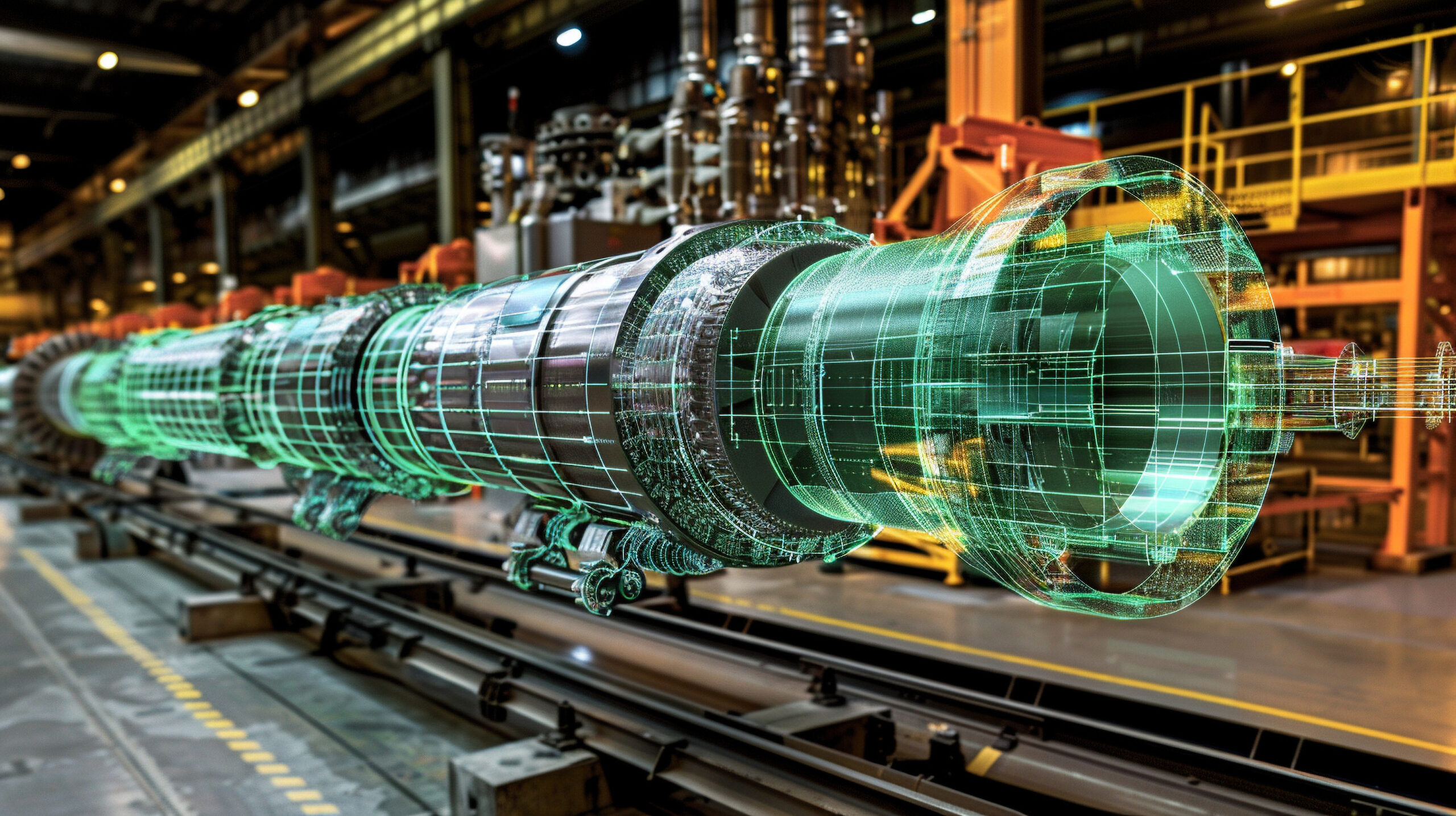
Réflexions | Simulation numérique et extrusion
Au cœur du câble il y a… l’extrusion. Un procédé de fabrication industriel thermo mécanique.
Le principe ? Un matériau, qui peut être un métal, du caoutchouc, des matières plastiques, des matériaux composites, se voient contraints de traverser une filière, ayant pour section la forme à obtenir. Il se fabrique ainsi en continu ce que l’on appelle un extrudat, en l’occurrence un produit long (tube, tuyau, profilé) ou plat (plaque, feuille, film).
Un procédé apparenté au tréfilage, mais qui fonctionne lui par effet de traction, et à froid.
Si l’extrusion est aujourd’hui incontournable dans l’industrie câblière c’est pour ses cadences de production. Et pour que la qualité reste au RDV je l’associe de plus en plus à de la simulation numérique. Mais avant de l’évoquer, je vous invite à une visite guidée au pays des trémies.
Qu’est-ce-que l’extrusion câblière ?
En câblerie, l’extrusion utilise notamment des granulés plastiques qui, une fois chauffés, vont se transformer en un liquide qui va s’écouler en continu. Et pour extruder il faut …une extrudeuse.
En l’occurrence :
une trémie, un entonnoir conique recueillant les granulés plastiques de base, additifs, colorants
un fourreau et une vis sans fin associés à des zones de chauffe pour que les granulés fondent et que le liquide visqueux soit transporté
une tête d’extrusion pour réaliser la forme autour des fils de cuivre ou des fibres optiques.
En plus de l’extrudeuse, d’autres éléments composent la ligne :
des dévidoirs ou dérouleurs pour débobiner les constituants du câble
des dispositifs de régulation de tension des composants
des bacs de refroidissement
des dispositifs de séchage, de marquage
une machine de tirage -cabestan ou chenille- régulée en tension
et un enrouleur pour stocker le câble fabriqué sur un touret.
Des systèmes de mesure et contrôle sont aussi déployés pour :
vérifier les diamètres en temps réel
détecter l’apparition d’excroissance, de trous
surveiller la vitesse et l’ensemble des paramètres de la ligne.
Une ligne d’extrusion qui pourra être dotée de systèmes de coextrusion (plusieurs extrudeuses connectées) en fonction des câbles et contraintes industrielles. Une technique qui permet de coextruder jusqu’à neuf couches de polymère, chacune ayant ses qualités propres, en utilisant plusieurs vis d’extrusion pour alimenter une même filière.
De fait, la fabrication d’un câble, tout comme sa conception, influe sur sa performance technico-économique. La complexité de la machine, l’organisation industrielle vont jouer. Quand on sait que chaque ligne d’extrusion nécessite un conducteur de ligne minimum, on comprend que ce coût doit être compensé par des taux de rendement synthétique (TRS) et des vitesses de lignes élevés. D’où les pistes d’extrusion « à grande vitesse ».
La grande vitesse est toujours possible mais contrainte par l’état de l’art et dépendante à la fois de la ligne d’extrusion, du choix des matières, de leur capacité à être transformées, et de l’opérateur.
Le design du produit fixé par le CDC client détermine le coût matières, leur capacité d’extrusion et conséquemment le design des outils de production car tous les accessoires sont importants dans cette chaine. Et quand on vise une montée en cadence, ils doivent suivre.
Or à dimensionnel fixe, une vitesse de ligne élevée génère des taux d’étirage et de cisaillement élevés ce qui nécessite l’adaptation des caractéristiques de la matière thermoplastique sélectionnée et la vérification des conséquences thermo chimiques et physiques sur le produit. Enfin, une LGV crée des contraintes sur le rythme de l’opérateur car un asservissement de ligne est indispensable pour sécuriser le lancement des productions et limiter la quantité de déchets lors des arrêts.
De fait, point d’accélération en matière d’extrusion à grande vitesse sans maîtrise exhaustive des designs et des coûts produits, alliée à une parfaite connaissance technique des lignes et une vraie maîtrise des comportements thermoplastiques des matières.
Côté coûts produits, la course au toujours plus petit
Au vu de ces contraintes, et sans surprise, miniaturiser, restreindre, alléger les #câbles est actuellement au cœur des évolutions technologiques. Le toujours plus petit -et léger- s’impose.
Les réseaux de #télécommunications à déployer doivent passer par les infrastructures existantes pour optimiser les coûts :
En souterrain dans des conduites déjà encombrées en repassant des câbles avec les autres -ce qui induit de vraies performances mécaniques en traction et frottement- ou en insérant des tubes plus petits, limitant encore l’espace, mais avec un moindre besoin de performance mécanique.
En aérien, en redéployant les câbles sur des poteaux déjà surchargés.
Dans les deux cas, limiter le poids et réduire les dimensions est une obligation.
Et pour y accéder différentes pistes sont travaillées.
👉Concernant la #fibre optique, l’optimisation des câbles passe par la réduction de la taille des fibres. La technologie s’appuie sur les propriétés des résines acrylates polymérisables UV qui sont les couches directes de protection de la fibre. Grâce à la contraction de leur épaisseur on passe de fibres standard de 245 micromètres (μm) de ⌀ à des fibres de qualité de 180/200 μm.
👉En parallèle, les loose tubes bénéficiant des performances optiques et dimensionnelles des fibres deviennent microloose avec des ⌀ de 1,2 mm, 1,4 et 1,6 mm contenant de 6 à 24 fibres. Idem pour les micromodules : Compact tube®, microgaine®, Flextube®. En septembre 2022 lors de Connected Britain, @WillyPelhate présentait en avant-première le nanomodule® : un module de 12 fibres de 250 μm de 1mm de ⌀ pour 1,33 mm pour son aïeul.
La construction des câbles incluant ces évolutions participe de fait à cette réduction globale et contribue au passage à alléger les impacts environnementaux.
👉Enfin, le dernier axe technologique concerne l’extrusion et les matériaux thermoplastiques. Les matériaux composites sont une piste de réflexion notamment les matériaux avec des fibres de renforcement en verre, carbone ou cristaux. On connait déjà les gaines HDPE renforcées par FRP ou ARP, pultrusion autour des fibres optiques, ou les structures composites de très faibles épaisseurs dont certaines utilisent des cristaux liquides.
Seule la connaissance fine des matériaux et de leurs comportements peut assurer la conservation des propriétés en fines épaisseurs. Associée à l’importance des modélisations matériaux en amont.
Connaissance des outillages, de leurs formes, des matières, des états de surface. Sans oublier l’interaction de la matière avec les outillages, les ajustements mécaniques de précision entre poinçon et filière, le bon dimensionnement des têtes d’extrusion et des vis pour optimiser les flux matières, la maitrise des conditions de refroidissement.
Bref, tout ce qui seul assure un usage non différencié au final sur le terrain.
Côté design produits, la simulation numérique comme adjuvant incontournable.
Concevoir un #câble à fibres optiques idéal n’est pas aussi simple qu’un coup de fil !
Si sur le terrain rien ne ressemble plus à un câble qu’un autre câble, les différentes rigidités, les différentes matières, les différentes fonctions des produits imposent l’utilisation de calculs de simulation et de modélisation. Et avant que cet ensemble d’éléments cylindriques ou tubulaires assemblés entre eux supporte le transport d’informations à près de 200 000 km/s, quelques règles s’imposent.
Première règle à ne jamais oublier, une #fibre optique est composée de verre et de résines acrylates. Elle est donc mécaniquement peu sensible aux effets de la température dans les plages normales d’utilisation (-40 +70°C). Ses caractéristiques de dilatation sont négligeables et elle ne présente pas de post retrait, relativement aux matériaux plastiques qui l’entourent.
Ensuite, quand elles sont libres -en micromodule ou loose tube- les fibres prennent une forme hélicoïdale, et leur longueur dans le module est, de fait, supérieure à la longueur du module lui-même.
Quant au diamètre intérieur du module, il est plus grand que le diamètre circonscrit à l’ensemble des fibres. Fibres dont il faut considérer qu’elles ondulent dans le module, au gré des signaux qui les traversent.
Voilà à quoi servent les calculs. Déterminer le diamètre optimal d’un module via la détermination de ce diamètre circonscrit.
Plusieurs méthodes de calculs existent mais la surfacique corrigée est celle que j’utilise le plus car elle donne des résultats relativement précis, surtout pour des éléments de petites dimensions.
Cette méthode consiste à additionner l’ensemble des sections de fibres du module pour en déterminer le diamètre équivalent. Par exemple, pour un module de 12 fibres de 250 µm de diamètre (df), le diamètre apparent (Da) sera Da = df x √ (12). A partir de Da, le diamètre circonscrit (Dc) à l’ensemble des 12 fibres est calculé en intégrant « les petits espaces vides entre les fibres ». Imaginons empiriquement que ces espaces vacants représentent 30% de la section totale contenue à l’intérieur de DC. Alors le diamètre circonscrit est obtenu en insérant un facteur 0,7 au dénominateur sous la racine, soit Dc = df x √ (12/0,7).
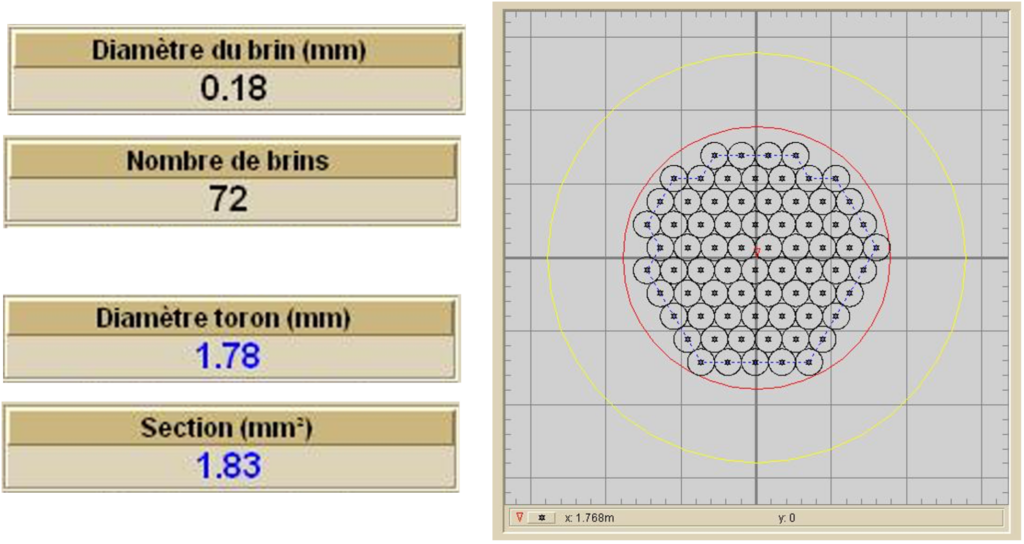
Les outils de simulation numérique actuels autorisent des calculs très précis concernant les dimensionnels. Ils sont donc des alliés de poids en ces heures de grande miniaturisation.
Mais poussons le curseur un cran plus avant, pour découvrir plus en détail comment la simulation numérique peut affiner le processus industriel, améliorer la qualité du design produit et éviter la surconsommation de matériau sur une chaîne d’extrusion.
L’apport de la simulation numérique en matière d’extrusion
Dans le domaine de l’extrusion, on s’appuie essentiellement sur de l’analyse paramétrique.
Cette analyse est réalisée par des moyens empiriques. Elle est basée sur les connaissances acquises par un personnel qualifié et s’appuie sur des phases de mise au point qui passent par la réalisation d’outils d’essais et augmentent les coûts et délais de fabrication.
Ceci étant, cette simulation numérique des procédés de mise en forme est un outil indispensable pour déterminer les paramètres de procédé optimaux.
En effet, elle améliore la compréhension du procédé de transformation de la matière plastique en donnant accès à des grandeurs physiques difficilement accessibles par l’expérience, parmi lesquelles la pression, la vitesse de cisaillement ou l’auto-échauffement.
Et en cela, la simulation numérique offre ainsi un gain de temps et une économie substantielle.
Car elle :
diminue le nombre d’expériences à mener permet d’analyser le procédé avant qu’il ne soit mis en œuvre.
La première étape est la modélisation de la géométrie des outils de transformation grâce aux éléments finis. La seconde consiste à déterminer des conditions de transformation avec paramétrage de calcul similaire à un paramétrage d’essai grandeur nature.
Dans le cadre de la compréhension du phénomène physique réel on peut donc « recopier » les paramètres appliqués sur la ligne :
pour lancer un calcul et scruter le comportement de la matière au cœur des outillages
constituer des sets de paramètres, issus par exemple d’une démarche de plan d’expérience, de type Taguchi
et caractériser par la suite les conditions optimales de transformation.
Dans un troisième temps on va modéliser le comportement de la matière, notamment lorsque la matière considérée n’est pas déjà présente dans la bibliothèque matériau du logiciel de simulation.
Cette modélisation est alors issue de l’analyse thermo-mécanique de la matière réalisée notamment avec un rhéomètre capillaire.
Enfin, les calculs de simulation sont lancés et pour obtenir des résultats en représentation 3D de la matière dans les outillages, parmi lesquels les vis, les distributeurs ou les têtes.
En chaque point, il est possible de déterminer pression, température, et vitesse. Et à ces points de mesure on peut également localiser l’origine des problèmes d’extrusion en les comparant à des seuils de cisaillement de la matière ou à des températures locales. Car il est à noter que différentes « anomalies » et problèmes qualité peuvent apparaitre durant l’extrusion :
des infondus,
la présence d’amas de matière « brulée »
ou des zones où le cisaillement est trop important
Les secondes étapes de calculs ont alors pour but de fixer les conditions optimales du process pour une matière et des outils considérés.
Le post retrait des matières plastiques est une vraie problématique de la transformation des matières plastiques. Et dans certains cas il peut être dangereux. Notamment lors de mise à nue d’un conducteur électrique sous tension. La maitrise des post retrait des matières plastique peut être atteinte grâce à la simulation numérique en évaluant les flux de matières dans les outillages et en vérifiant que les seuils de cisaillement ne sont jamais dépassés.
Alors que l’heure nous enjoint à la miniaturisation, la simulation nous offre la précision.
Une simulation numérique appliquée à l’extrusion pour avoir la maitrise de la transformation grâce à la production d’informations à l’intérieur des outils de transformation. Et pour accéder à une meilleure connaissance et un meilleur traitement de l’instabilité de certains comportements, qu’ils soient mécaniques ou physico-chimiques sur l’ensemble de la chaîne d’extrusion.
Associée à des plans d’expérience, elle évite un grand nombre d’essais et accélère le développement des produits, sans pour autant remplacer la réalisation pour validation. Et détermine des sets de paramètres optimisés pour une production industrielle alliant qualité et efficience !
N’est-ce pas là ce que nous voulons collectivement obtenir pour notre belle industrie câblière ?